
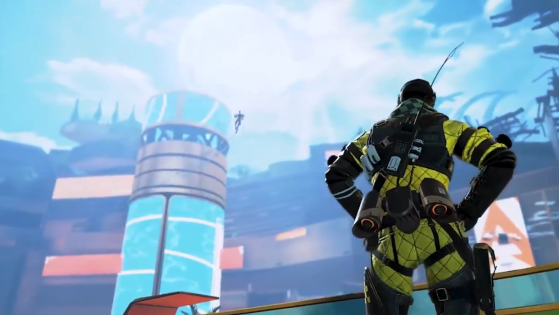
Further advantageous embodiments and useful developments of the present invention become apparent from the description below. It is a particular object of the present invention to provide solution to the above problems by a method in accordance with the features described herein, as well as a blade repair element designed in accordance with the features described herein for the performance of the method. In a broad aspect, the present invention provides for a reduction of the work effort and costs for blisk repair, and for an appropriate method and means for the performance of this method, with this method also being applicable to the new manufacture of blisks. In addition, the effort for technical assessment of the quality of the repaired blades or blisks is high.

Quality defects in blisk repair can, therefore, not be excluded.
#BLISK LIES MANUAL#
The repair of blisks by cutting off and either subsequent multi-pass welding or individual manufacture of the corresponding insert and correct manual positioning and fixation of the latter in the limited space available between the blades incurs considerable effort. According to yet another feature of this method, an individually pre-manufactured insert, whose shape and size correspond to the cutout, can first be tack-welded to or located by suitable fixtures in the right position on the edge of the cutout, and subsequently be firmly joined to the blade in a welding process. Subsequently, the recess is re-filled with several weld passes in a suitable welding process and machined. 6,568,077, a certain area of the leading or trailing edge of the damaged rotor blades is cut off in dependence of previously determined stress lines in such a manner that the cutout is clear of the areas of maximum stress in the blade. In a method for the repair of damaged blisks known from U.S. This advantageous, but expensive, approach is not possible with compressors in blisk technology as their rotor blades are one piece with the rotor disk. If the rotor blades are manufactured separately and attached separably to the rotor disk, the damaged or worn blades can relatively easily be replaced by new ones. Moreover, the blade leading edge, in particular, is liable to damage by larger objects, but also by small stones. The compressor blades of aircraft engines are, as is generally known, subject to considerable erosion in the area of the tip edge and-if the sand particle content of the air is high-also in a zone reaching from the tip edge to the trailing edge. This has positive consequences, for example on the weight and the performance of the engine. In comparison with compressors whose blades are separately manufactured and separably attached to the rotor disk, the one-piece blisks are advantageous in that they are capable of withstanding higher mechanical loads. The compressors of aircraft engines are, in many cases, designed in blisk technology, with the rotor blades being integral with the rotor disk. Moreover, the present invention relates to the new manufacture of blisks. This invention relates to a method for the repair of blisks in which the damaged blade section is removed and replaced by a new blade portion of corresponding shape and size by welding, and to a blade repair element for the performance of the method. 30, 2004, the entirety of which is incorporated by reference herein. This application claims priority to German Patent Application DE102004032461.1 filed Jun.
